My blog focuses on Business/Entrepreneurship and Workplace Discussions. Manufacturing is a critical sector in most countries. Safety is still of the utmost importance in this sector. The following contributed post is entitled, Manufacturing Safety Still Has A Long Way To Go.
* * *
In 2019 alone, the manufacturing industry in the United States reported a staggering 846,700 injuries, a figure that paints a troubling picture of the risks workers still face daily. While many industries have made progress in safety procedures and awareness, manufacturing continues to rank among the most hazardous fields. And it raises a vital question: with all the data and tools at our disposal, why is the number still so high?
The truth is, most accidents aren’t mysterious. We know where the cracks are. And more often than not, the causes are preventable. In other words, the right structure in place could save the lives of many in the manufacturing industry. So why aren’t they here already?
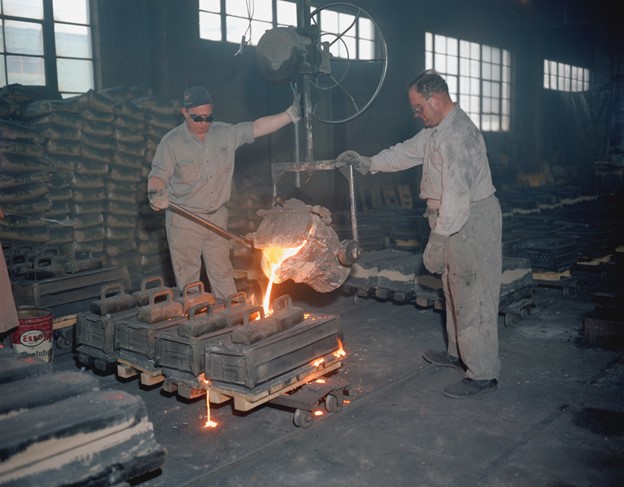
Lack of Proper Training
Too often, safety training is treated as a one-time event. In fast-paced environments where deadlines are tight, formal safety instruction is frequently overlooked in favor of learning on the job.
But skipping proper training has long-term consequences. Workers are more likely to make small mistakes that lead to serious injuries.
Ongoing, hands-on instruction is essential. That means building regular safety refreshers into the schedule and creating a system of peer mentoring where more experienced workers reinforce best practices. A strong foundation in employee training is one of the most effective ways to reduce risk across the board.
Improper Handling of Heavy Loads
In manufacturing, lifting and transporting heavy loads is part of daily operations, but when proper tools aren’t provided or are in disrepair, workers are often forced to improvise.
That might mean lifting without assistance, relying on worn-out straps or ropes, or using equipment not rated for the weight being moved.
Cutting corners to save time or money may seem cost- and time-effective in the short term, but the cost of injury is far greater, both physically and financially. Companies should invest in lifting gear that’s designed for the task. Simple tools like chain slings can drastically reduce the risk when handling heavy materials.
Communication Gaps in the Workplace
No safety strategy is complete without communication. Yet in many manufacturing plants, the flow of information is either top-down or unclear. Workers may hesitate to report hazards for fear of being blamed or ignored. Others may not fully understand protocols due to language barriers or lack of access to resources.
When safety becomes a shared conversation that welcomes feedback, it becomes part of the culture. Regular team huddles, anonymous reporting channels, and open-door policies all help bridge the gap. Safety signage and instructions should be multilingual and clearly visible. Most importantly, leadership needs to model the behavior they want to see. In other words, when the management cuts corners, the employees will too.
In conclusion, we often hear that “safety is everyone’s responsibility”, and the statement still holds true. But the responsibility doesn’t start with the employees. It starts with leadership and is sustained by commitment across the board about safety every day matters.
Real change in workplace safety in the manufacturing sector comes from investing in people and systems that make it easier to do the right thing. When workers are trained, equipped, and heard, the statistics can finally begin to shift.