Three focuses of my blog are Financial Literacy/Money, Business/Entrepreneurship and Technology. We are in the age automation and technology performing jobs once performed by man. If you are thinking about going into business of some sort, this is a very important consideration. The following contributed post is entitled, The Power Of Automation In Business.
* * *
In the rapidly changing business world, automation is transforming Industries. Companies are using automation tools to streamline their operations, improve efficiency and reduce costs. However, understanding how and where you should use automation as a business can be challenging, especially in sectors where precision is critical such as manufacturing life sciences and Pharmaceuticals.
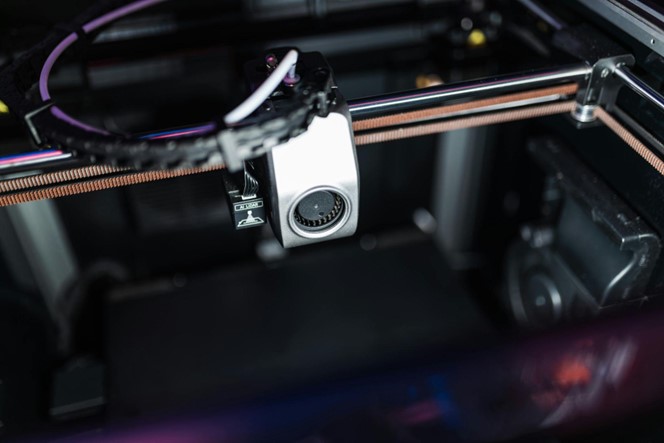
Photo by Matheus Bertelli: https://www.pexels.com/photo/3d-printer-with-camcorder-20877036/
The Benefits Of Automation
Automation provides businesses with many key benefits. It significantly reduces the time that I spend on repetitive tasks by automating routine processes such as inventory management reporting and data entry. Companies can, therefore, free up the time I’ve valuable employees to focus on more important tasks that add value to the business. It not only improves the productivity of the company but also improves job satisfaction as work is less bogged down by mundane, repetitive work.
Automation also works to improve accuracy and reduce the risk of human error. In fields such as manufacturing or laboratory testing, even a minor mistake can have a serious impact. Automated systems can handle large volumes of tasks or data with precision, which minimises the risk of errors and ensures consistent results. This is especially important in industries that need to comply with regulations.
Automation also leads to cost savings. Even though the initial investment in automation technology might be a significant impact on the business the long-term savings and return on investment is something that you can’t turn away.
Precision Automation In Sciences
In industries like life sciences, precision automation is a vital part of the process. Companies need to make sure that research testing and production are all conducted with high levels of accuracy. When you use automated systems not only reduces the margin for error but it also enables businesses to have a faster turnaround time. This is a critical improvement when it comes to meeting deadlines in production and research.
Tacan, a global provider of laboratory automation systems, is a key player in this field. The advanced technologies enable Laboratories to automate complex testing processes and make them receive faster and more reliable results. If you are a business that works in life sciences, investing in automation Solutions like those offered by Tecan can significantly improve outcomes and Efficiency.
Key Considerations When Implementing Automation
Before you introduce automation to your business, you need to think about several factors to ensure that it is successful. First, you need to evaluate the processes that you have in your business and which ones are most suited to automation. Repetitive tasks that require you to have high accuracy and be consistent are ideal for automation. You need to ensure that the technology you are using integrates seamlessly with your existing systems and workflows so that you aren’t causing any unneeded disruptions. Another important consideration you need to make is employee training, which may be required to use any of the automated systems.
In conclusion, automation is something that businesses should be using to enhance productivity, save on costs, and improve accuracy; however, they need to make sure they are choosing the right areas to automate and position themselves for long-term success.