My blog focuses on Health/Wellness and Workplace Discussions. Manufacturing has some unique health-related functions and scenarios. It’s critical to know what they are and how to avoid them. The following contributed post is entitled, The Worst Quality Hazards Of Healthcare Manufacturing, And How To Avoid Them.
* * *
Quality compromises are always bad news in manufacturing, but never do they have such a significant impact as within the field of healthcare. After all, you aren’t simply creating products within your healthcare business. You’re developing potentially life-saving equipment, and even minor issues could have fatal consequences.
The careful management of all areas of healthcare manufacturing is therefore key. But what are the worst quality hazards to look out for, and what steps should you take to avoid them at all costs?
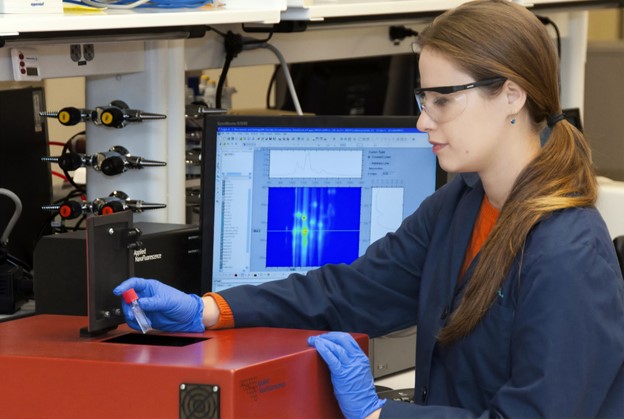
# 1 – Quality Control Failures
Quality control processes, which involve ensuring that products meet a range of predetermined standards, should always be a vital manufacturing element. This is how you ensure that all products leaving your factory are fit for purpose and unlikely to let your brand down. In the healthcare industry, this is also how you ensure that your products save lives rather than endanger them.
Unfortunately, there are many ways to slip into catastrophic quality control failures, including failing to effectively delegate or document this process. Let’s say that you’re manufacturing hospital beds. Somewhere during the manufacturing process, there was an error with the custom torsion spring that’s responsible for the integrity of those beds. But your quality control processes are haphazard and poorly tracked, so everyone assumes someone else has checked everything over and found no problems. The beds are sent out and instantly collapse, causing further harm to potentially elderly or injured patients.
As well as leaving you at risk of noncompliance and the hefty associated fines, this throws your manufacturing integrity under serious question. Don’t let that happen. Instead, always prioritize well-handled quality control processes with multiple checkpoints and proper, traceable documentation that’s easily accessible for everyone.
# 2 – Confused Training Focuses
Specialized training is vital in a warehouse that handles potentially hazardous medical chemicals, and should be provided across all relevant team members. Unfortunately, too many healthcare manufacturers slip into confusion about who those team members might be. This can result in training oversights, particularly within management teams who can too often leave themselves off the register. Risks can very quickly follow including non-conformance and the risk of dangerous exposure.
As a rule, all team members overseeing a process or procedure should receive adequate training, even if they’re not directly involved themselves. That means your higher-management team, as well as your on-ground employees, should always be in that training room.
# 3 – Sterility Risks
Sometimes, healthcare manufacturing hazards come in the form of lacking sterility that sees products failing to meet the FDA’s aseptic standards and International Organization for Standardization (ISO) regulations. This most commonly arises when medical device packaging becomes unsterile for reasons including exposure and poor design.
Obviously, changing your processes to ensure improved cleaning and sterility checks can manage exposure risks. Packaging design is a little harder to handle, but The National Library of Medicine has found that additions like outward curling seals can significantly reduce sterility risks.
Medical manufacturing can easily feel like a minefield, but avoiding these quality hazards can help you get ahead.