Two focuses of my blog are Technology and Workplace Discussions. If you’re running a business or workplace that utilizes equipment of any kind, the upkeep of that equipment should be of your utmost concern. The following contributed post is entitled, What Are The Common Causes Of Equipment Failure?
* * *
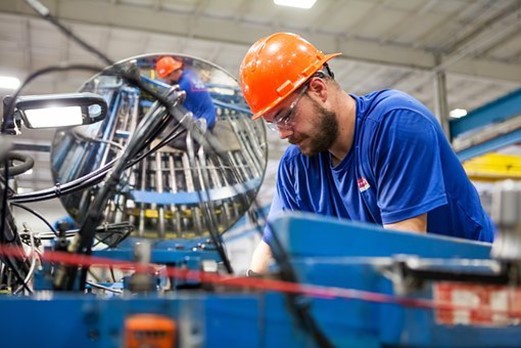
Machine or equipment failures are very common. However, high repair costs, health and safety concerns, and poor service delivery can harm your business. The world’s biggest manufacturing firms lose almost $1 trillion annually due to machine failures! As a business owner, you should expect your equipment to break down from time to time. But you can prevent the frequency by understanding the factors that cause your machines to reduce their efficiency. Here are three common causes of equipment failure you should know.
1. Lack of technical know-how
Several people come around your equipment regularly whose actions could have a huge impact on its performance. Machine operators are usually the ones to operate machines the most. When they are properly trained, these operators can understand operation procedures, conduct basic trouble to solve any minor malfunction, and know the health and safety practices to adopt when operating machines.
On the other hand, an operator that has not been rigorously trained and doesn’t fully understand why or how a machine works is likely to cause significant damage to it. You must organize regular training sessions for operators to always prepare for unexpected or new issues. At the very least, they would be able to identify issues that are beyond their skills and report them. As a business owner, you must never permit an operator to use a machine they are not qualified to run.
2. Poor maintenance
Poor maintenance is one of the leading causes of equipment failure. Most machines need regular maintenance to ensure that it performs at their optimum. However, most businesses fail to conduct regular maintenance checks, especially when things seem to be running fine, and they assume that operators would bring up any potential issues. Unfortunately, that’s not the way to go. It isn’t easy to spot early signs of dwindling performance and efficiency. Regular maintenance helps you track your machine’s performance making it easier to identify subtle changes.
As a business owner, preventative maintenance is your best approach to ensuring that your machines don’t fail. It reduces your downtown by up to 75%. Regular tune-ups will extend your machine’s lifespan. You must also train your operators to identify the standard components for mechanical parts that need replacements.
3. Overworking your machines
When you purchase your equipment, you want to get the most out of its functions. That means you have to run them at their peak performance level. However, overworking your machines can cause them to break down much earlier than they should. Setting its performance at the highest all the time can put a massive strain on its components. Instead, ensure that you and the other machine operators understand how your machine works and how to set its performance based on the type of job it has to do.
Although extremely useful, machines can be very unpredictable. Therefore, it is important to familiarize yourself with some of the potential causes of their breakdown and identify ways to reduce such occurrences, so that your business doesn’t suffer.