My blog focuses on Science, Technology, Engineering and Mathematics (STEM) and Technology. Of the elements on the periodic table, an underappreciate member is Tungsten. This element likewise has many uses to us. The following contributed post is entitled, Why Aren’t We Using More Tungsten.
* * *
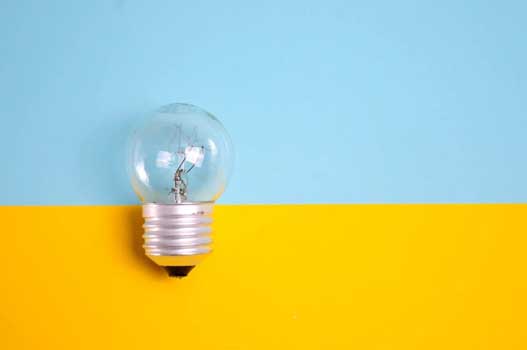
Tungsten is a type of metal you usually find on the end of drill bits and in high-intensity applications. The metal is known for being extremely hard, and many measurements put it second only to diamond.
But, strangely, the world doesn’t use much of the stuff. Yes, it does have applications in industry and the trades. But given its extreme durability, you’d expect to see it in more places.
For example, carbide bushings are used in numerous high-friction environments and industrial processes. These are well-known for lasting up to ten times longer than steel, and yet many manufacturers still prefer to use the latter.
The same applies to cheap tools. Many believe in a false economy that tungsten is expensive.
Processing Challenges
One reason for using less tungsten has to do with its hardness. While steel is relatively easy to shape, tungsten isn’t, meaning it is more difficult for manufacturers to shape it into usable items. When combined with carbide, it becomes even tougher, meaning that only the highest-quality processes can manipulate it.
Processing challenges add to production costs, but they don’t detract from the quality of the finished product, same as titanium. The methods are well understood, they just require additional energy input.
Rarity
Rarity is another leading reason people don’t use as much tungsten as they would like. The stuff isn’t as common in the Earth’s crust as iron.
Most tungsten comes from wolframite and scheelite using intensive, energy-consuming processes. The total amount of the metal that can come out of each piece of ore is lower than many people expect.
For this reason, tungsten can be more expensive. But, of course, it lasts many times longer than steel in standard operations, meaning that it is usually economical to get it anyway.
Titanium Alloys
Some manufacturers are also trying to use titanium alloys instead of tungsten. These are hard, but they still don’t have the extreme hardness that tungsten offers. Other benefits include corrosion resistance, but these still apply to tungsten in heavyweight applications.
Density
The density of tungsten is a legitimate concern in some applications. The aerospace sector doesn’t use the metal because it is too heavy for most jet engines to get off the ground. It’s also not particularly in demand in the automotive sector, other than for the odd piece of equipment here and there in high-intensity applications.
There are some niche areas, though, where it makes sense. Oil rigs, for instance, make extensive use of tungsten. So too do coolant systems and drills.
The answer to why we aren’t using more tungsten is, therefore, a complex one. On the one hand, you have the issue of failing to understand the economics, but on the other, you also have cost and rarity.
Ultimately, it comes down to a cost-benefit analysis. In some applications, tungsten is massively underutilized, while in others, it doesn’t make as much sense to include it.
Given its hardness, it should become more of a feature in products designed to last for decades.